Yarımkeçiricilərin istehsalı prosesində kritik bir addım kimi vafli dilimləmə texnologiyası çip performansı, məhsuldarlıq və istehsal xərcləri ilə birbaşa bağlıdır.
# 01 Gofret Kəsmənin Əsası və Əhəmiyyəti
1.1 Vafli dilimləmənin tərifi
Vafli dilimləmə (həmçinin cızma kimi tanınır) yarımkeçirici istehsalında vacib bir addımdır və işlənmiş vafli çoxlu fərdi kalıplara bölmək məqsədi daşıyır. Bu kalıplar adətən tam dövrə funksionallığını ehtiva edir və elektron cihazların istehsalında istifadə olunan əsas komponentlərdir. Çip dizaynları daha mürəkkəbləşdikcə və ölçülər kiçilməyə davam etdikcə, vafli dilimləmə texnologiyası üçün dəqiqlik və səmərəlilik tələbləri getdikcə daha sərt olur.
Praktiki əməliyyatlarda, vafli dilimləmə adətən almaz bıçaqlar kimi yüksək dəqiqlikli alətlərdən istifadə edir ki, hər bir zərfin toxunulmaz və tam funksional qalması təmin edilir. Əsas addımlara kəsmə əvvəli hazırlıq, kəsmə prosesi zamanı dəqiq nəzarət və kəsildikdən sonra keyfiyyətin yoxlanılması daxildir.
Kəsmədən əvvəl vafli dəqiq kəsmə yollarını təmin etmək üçün işarələnməli və yerləşdirilməlidir. Kəsmə zamanı vaflinin zədələnməsinin qarşısını almaq üçün alətin təzyiqi və sürəti kimi parametrlərə ciddi şəkildə nəzarət edilməlidir. Kəsmədən sonra hər çipin performans standartlarına cavab verməsini təmin etmək üçün hərtərəfli keyfiyyət yoxlamaları aparılır.
Vafli dilimləmə texnologiyasının əsas prinsipləri təkcə kəsici avadanlıqların seçilməsi və proses parametrlərinin təyin edilməsini deyil, həm də materialların mexaniki xassələrinin və xüsusiyyətlərinin kəsmə keyfiyyətinə təsirini əhatə edir. Məsələn, aşağı k-li dielektrik silikon vaflilər, aşağı mexaniki xassələrinə görə, kəsmə zamanı gərginlik konsentrasiyasına çox həssasdır və bu, qırılma və çatlama kimi uğursuzluqlara səbəb olur. Aşağı k materialların aşağı sərtliyi və kövrəkliyi onları mexaniki qüvvə və ya istilik gərginliyi altında, xüsusən də kəsmə zamanı struktur zədələnməsinə daha çox meylli edir. Alət və vafli səthi arasındakı təmas, yüksək temperaturla birlikdə stress konsentrasiyasını daha da gücləndirə bilər.
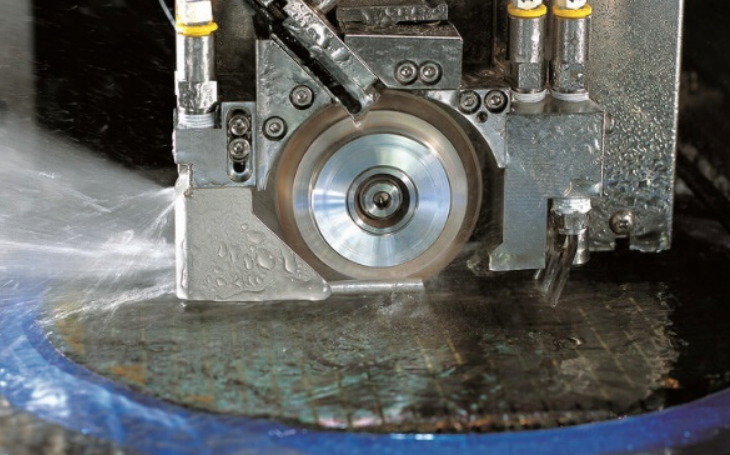
Material elmindəki irəliləyişlərlə, vafli dilimləmə texnologiyası, qallium nitridi (GaN) kimi yeni materialları daxil etmək üçün ənənəvi silikon əsaslı yarımkeçiricilərdən kənara çıxdı. Bu yeni materiallar öz sərtliyinə və struktur xüsusiyyətlərinə görə kəsici alətlər və texnikanın daha da təkmilləşdirilməsini tələb edən küp kəsmə prosesləri üçün yeni problemlər yaradır.
Yarımkeçiricilər sənayesində kritik bir proses olaraq, vaflilərin kəsilməsi, gələcək mikroelektronika və inteqral sxem texnologiyaları üçün zəmin yaratmaqla, inkişaf edən tələblərə və texnoloji irəliləyişlərə cavab olaraq optimallaşdırılmağa davam edir.
Vafli dilimləmə texnologiyasındakı təkmilləşdirmələr köməkçi materialların və alətlərin hazırlanmasından kənara çıxır. Onlar həmçinin prosesin optimallaşdırılmasını, avadanlığın işində təkmilləşdirmələri və kəsmə parametrlərinə dəqiq nəzarəti əhatə edir. Bu irəliləyişlər yarımkeçiricilər sənayesinin daha kiçik ölçülərə, daha yüksək inteqrasiyaya və daha mürəkkəb çip strukturlarına olan ehtiyacını ödəməklə, vafli dilimləmə prosesində yüksək dəqiqliyi, səmərəliliyi və sabitliyi təmin etmək məqsədi daşıyır.
yaxşılaşdırma sahəsi | Xüsusi tədbirlər | Effektlər |
Proseslərin optimallaşdırılması | - Daha dəqiq vafli yerləşdirmə və yolun planlaşdırılması kimi ilkin hazırlıqları təkmilləşdirin. | - Kəsmə xətalarını azaldın və sabitliyi yaxşılaşdırın. |
- Kəsmə xətalarını minimuma endirmək və sabitliyi artırmaq. | - Alətin təzyiqini, sürətini və temperaturunu tənzimləmək üçün real vaxt rejimində monitorinq və əks əlaqə mexanizmlərini qəbul edin. | |
- Gofret qırılma dərəcələrini aşağı salın və çip keyfiyyətini yaxşılaşdırın. | ||
Avadanlıq Performansının Təkmilləşdirilməsi | - Yüksək dəqiqlikli mexaniki sistemlərdən və qabaqcıl avtomatlaşdırma idarəetmə texnologiyasından istifadə edin. | - Kəsmə dəqiqliyini artırın və material itkisini azaldın. |
- Yüksək sərtlikli material vafliləri üçün uyğun lazer kəsmə texnologiyasını tətbiq edin. | - İstehsalın səmərəliliyini artırmaq və əl səhvlərini azaltmaq. | |
- Avtomatik monitorinq və tənzimləmələr üçün avadanlığın avtomatlaşdırılmasını artırın. | ||
Dəqiq Parametrə Nəzarət | - Kəsmə dərinliyi, sürət, alət növü və soyutma üsulları kimi parametrləri incə şəkildə tənzimləyin. | - Kalıbın bütövlüyünü və elektrik performansını təmin edin. |
- Vafli materialı, qalınlığı və quruluşu əsasında parametrləri fərdiləşdirin. | - Məhsuldarlığı artırın, material tullantılarını azaldın və istehsal xərclərini azaldın. | |
Strateji əhəmiyyəti | - Davamlı olaraq yeni texnoloji yolları araşdırın, prosesləri optimallaşdırın və bazar tələblərinə cavab vermək üçün avadanlıq imkanlarını artırın. | - Yeni materialların və qabaqcıl çip dizaynlarının işlənib hazırlanmasını dəstəkləyərək, çip istehsalının məhsuldarlığını və performansını yaxşılaşdırın. |
1.2 Vafli dilimləmənin əhəmiyyəti
Vafli dilimləmə yarımkeçiricilərin istehsalı prosesində mühüm rol oynayır, sonrakı addımlara, eləcə də son məhsulun keyfiyyətinə və performansına birbaşa təsir göstərir. Onun əhəmiyyətini aşağıdakı kimi təfərrüatlandırmaq olar:
Birincisi, kəsmənin dəqiqliyi və ardıcıllığı çip məhsuldarlığını və etibarlılığını təmin etmək üçün açardır. İstehsal zamanı vaflilər çox sayda mürəkkəb dövrə strukturları yaratmaq üçün bir neçə emal mərhələsindən keçirlər ki, bu da fərdi fişlərə (pərəstlərə) dəqiq bölünməlidir. Küp kəsmə prosesində hizalama və ya kəsmə zamanı əhəmiyyətli səhvlər olarsa, sxemlər zədələnə bilər və bu, çipin funksionallığına və etibarlılığına təsir göstərə bilər. Buna görə də, yüksək dəqiqlikli kub kəsmə texnologiyası yalnız hər bir çipin bütövlüyünü təmin etmir, həm də daxili dövrələrin zədələnməsinin qarşısını alır, ümumi məhsuldarlığı artırır.
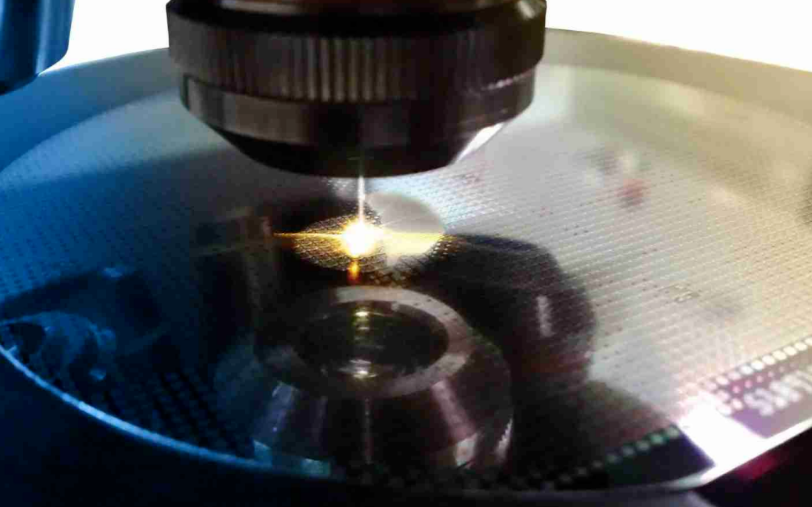
İkincisi, vafli dilimləmə istehsalın səmərəliliyinə və xərclərə nəzarətə əhəmiyyətli təsir göstərir. İstehsal prosesində həlledici addım kimi onun səmərəliliyi sonrakı mərhələlərin gedişatına birbaşa təsir göstərir. Küp kəsmə prosesini optimallaşdırmaq, avtomatlaşdırma səviyyələrini artırmaq və kəsmə sürətlərini təkmilləşdirməklə ümumi istehsal səmərəliliyini xeyli artırmaq olar.
Digər tərəfdən, kəsmə zamanı material itkisi xərclərin idarə edilməsində mühüm amildir. Qabaqcıl doğrama texnologiyalarından istifadə yalnız kəsmə prosesi zamanı lazımsız material itkilərini azaltmaqla yanaşı, vafli istifadəni də artırır və bununla da istehsal xərclərini azaldır.
Yarımkeçirici texnologiyasındakı irəliləyişlərlə, vafli diametrləri artmağa davam edir və dövrə sıxlıqları müvafiq olaraq yüksəlir, bu da kəsmə texnologiyasına daha yüksək tələblər qoyur. Daha böyük vaflilər kəsici yollara daha dəqiq nəzarət tələb edir, xüsusən də kiçik sapmaların çoxlu çipləri qüsurlu edə biləcəyi yüksək sıxlıqlı dövrə sahələrində. Bundan əlavə, daha böyük vaflilər daha çox kəsmə xətlərini və daha mürəkkəb proses addımlarını ehtiva edir ki, bu da bu çağırışlara cavab vermək üçün kəsmə texnologiyalarının dəqiqliyi, ardıcıllığı və səmərəliliyinin daha da təkmilləşdirilməsini tələb edir.
1.3 Gofret Kəsmə Prosesi
Vafli dilimləmə prosesi hazırlıq mərhələsindən son keyfiyyət yoxlamasına qədər bütün mərhələləri əhatə edir və hər bir mərhələ doğranmış çipslərin keyfiyyətini və performansını təmin etmək üçün vacibdir. Aşağıda hər bir mərhələnin ətraflı izahı verilmişdir.
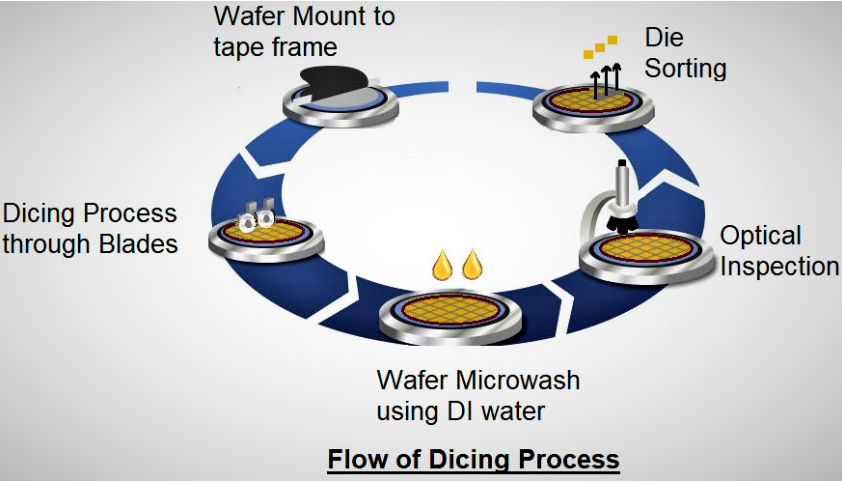
Faza | Ətraflı təsvir |
Hazırlıq mərhələsi | -Gofretin təmizlənməsi: Təmiz səthi təmin edərək çirkləri, hissəcikləri və çirkləndiriciləri təmizləmək üçün ultrasəs və ya mexaniki ovma ilə birlikdə yüksək saflıqda su və xüsusi təmizləyici vasitələrdən istifadə edin. -Dəqiq Yerləşdirmə: Vaflinin nəzərdə tutulmuş kəsmə yolları boyunca dəqiq bölünməsini təmin etmək üçün yüksək dəqiqlikli avadanlıqdan istifadə edin. -Gofret fiksasiyası: Kəsmə zamanı sabitliyi qorumaq, vibrasiya və ya hərəkət nəticəsində zədələnməmək üçün vafli lent çərçivəsinə bərkidin. |
Kəsmə mərhələsi | -Blade Dicing: Fiziki kəsmə üçün yüksək sürətli fırlanan almazla örtülmüş bıçaqlardan istifadə edin, silikon əsaslı materiallar üçün uyğun və sərfəli. -Lazer kəsmə: Təmassız kəsmə üçün yüksək enerjili lazer şüalarından istifadə edin, qallium nitridi kimi kövrək və ya yüksək sərtliyə malik materiallar üçün idealdır, daha yüksək dəqiqlik və daha az material itkisi təklif edir. -Yeni Texnologiyalar: İstilikdən təsirlənən zonaları minimuma endirərkən səmərəliliyi və dəqiqliyi daha da artırmaq üçün lazer və plazma kəsmə texnologiyalarını tətbiq edin. |
Təmizləmə mərhələsi | - Kəsmə zamanı yaranan zibil və tozu təmizləmək üçün qalıqların sonrakı proseslərə və ya çiplərin elektrik performansına təsir etməsinin qarşısını almaq üçün ultrasəs və ya sprey təmizləmə ilə birlikdə deionlaşdırılmış su (DI su) və xüsusi təmizləyici vasitələrdən istifadə edin. - Yüksək təmizlikli DI suyu təmiz vafli mühiti təmin edərək yeni çirkləndiricilərin daxil olmasının qarşısını alır. |
Yoxlama mərhələsi | -Optik yoxlama: Qüsurları tez bir zamanda müəyyən etmək, doğranmış çiplərdə çatların və ya qırılmaların olmaması, yoxlamanın səmərəliliyini artırmaq və insan səhvini azaltmaq üçün AI alqoritmləri ilə birlikdə optik aşkarlama sistemlərindən istifadə edin. -Ölçü Ölçüsü: Çip ölçülərinin dizayn spesifikasiyalarına uyğun olduğunu yoxlayın. -Elektrik Performans Testi: Sonrakı tətbiqlərdə etibarlılığı təmin edərək, kritik çiplərin elektrik performansının standartlara uyğun olmasını təmin edin. |
Çeşidləmə mərhələsi | - İxtisaslı çipləri lent çərçivəsindən ayırmaq üçün robot qolları və ya vakuum sorma stəkanlarından istifadə edin və onları performansa görə avtomatik çeşidləyin, istehsal səmərəliliyini və çevikliyi təmin edərək, dəqiqliyi artırın. |
Vafli kəsmə prosesi vaflitin təmizlənməsini, yerləşdirilməsini, kəsilməsini, təmizlənməsini, yoxlanılmasını və çeşidlənməsini əhatə edir, hər bir addım kritikdir. Avtomatlaşdırma, lazer kəsmə və AI yoxlama texnologiyalarında irəliləyişlərlə müasir vafli kəsmə sistemləri daha yüksək dəqiqliyə, sürətə və daha az material itkisinə nail ola bilər. Gələcəkdə lazer və plazma kimi yeni kəsmə texnologiyaları getdikcə mürəkkəbləşən çip dizaynlarının ehtiyaclarını ödəmək üçün ənənəvi bıçaq kəsməni tədricən əvəz edəcək və yarımkeçiricilərin istehsalı proseslərinin inkişafına təkan verəcək.
Vafli Kəsmə Texnologiyası və Onun Prinsipləri
Şəkil üç ümumi vafli kəsmə texnologiyasını göstərir:Blade Dicing,Lazer kəsmə, vəPlazma kəsmə. Aşağıda bu üç texnikanın ətraflı təhlili və əlavə izahı verilmişdir:
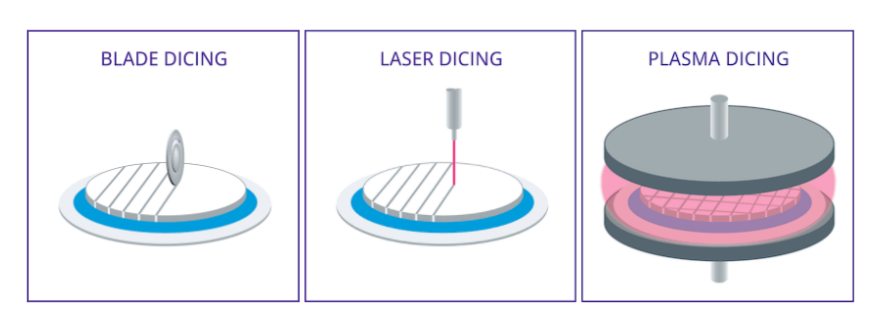
Yarımkeçirici istehsalda vaflinin kəsilməsi vaflinin qalınlığına əsaslanaraq müvafiq kəsmə üsulunun seçilməsini tələb edən mühüm addımdır. İlk addım vaflinin qalınlığını təyin etməkdir. Gofretin qalınlığı 100 mikrondan çox olarsa, kəsmə üsulu olaraq bıçaqların kəsilməsi seçilə bilər. Bıçaqla kəsmə uyğun deyilsə, sınıq dilimləmə üsulundan istifadə edilə bilər ki, bu üsul həm yazıcı kəsmə, həm də bıçaqla kəsmə üsullarını əhatə edir.
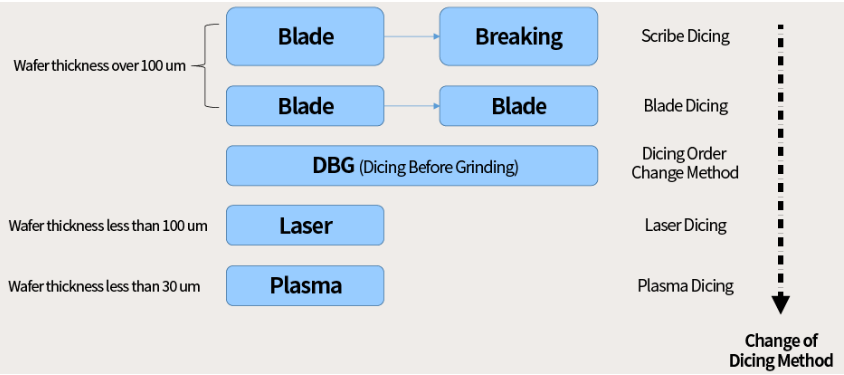
Gofretin qalınlığı 30 ilə 100 mikron arasında olduqda, DBG (Dice Before Grinding) üsulu tövsiyə olunur. Bu halda, ən yaxşı nəticələrə nail olmaq üçün zərurət yarandıqda yazı kəsmə, bıçaq kəsmə və ya kəsmə ardıcıllığını tənzimləmək seçilə bilər.
Qalınlığı 30 mikrondan az olan ultra nazik vaflilər üçün, həddindən artıq zədələnmədən nazik vafliləri dəqiq şəkildə kəsmək qabiliyyətinə görə lazerlə kəsmə üstünlük verilən üsula çevrilir. Lazer kəsmə xüsusi tələblərə cavab verə bilmirsə, alternativ olaraq plazma kəsmə istifadə edilə bilər. Bu axın sxemi müxtəlif qalınlıq şəraitində ən uyğun vafli kəsmə texnologiyasının seçilməsini təmin etmək üçün aydın qərar qəbuletmə yolunu təqdim edir.
2.1 Mexaniki kəsmə texnologiyası
Mexanik kəsmə texnologiyası vafli dilimləmədə ənənəvi üsuldur. Əsas prinsip vafli dilimləmək üçün kəsici alət kimi yüksək sürətli fırlanan almaz daşlama çarxından istifadə etməkdir. Əsas avadanlıqlara əvvəlcədən müəyyən edilmiş kəsmə yolu boyunca dəqiq kəsmə və ya yiv açmağı yerinə yetirmək üçün almaz daşlama çarxını yüksək sürətlə idarə edən hava daşıyan mil daxildir. Bu texnologiya aşağı qiymətə, yüksək effektivliyə və geniş tətbiq qabiliyyətinə görə sənayedə geniş istifadə olunur.
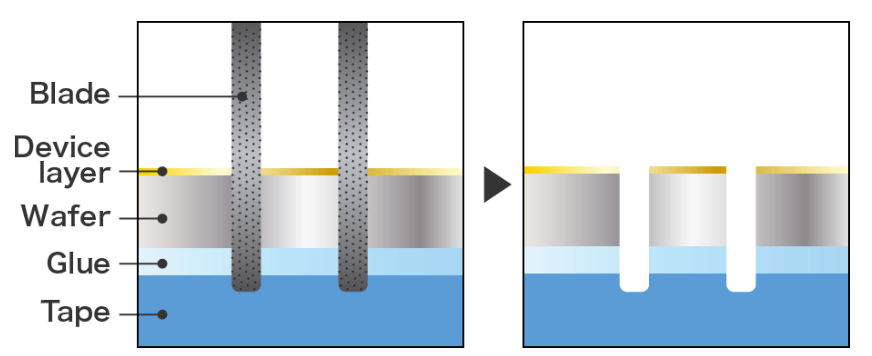
Üstünlüklər
Almaz daşlama çarxlarının yüksək sərtliyi və aşınma müqaviməti mexaniki kəsmə texnologiyasına müxtəlif vafli materialların, istər ənənəvi silikon əsaslı materiallar və ya daha yeni mürəkkəb yarımkeçiricilərin kəsmə ehtiyaclarına uyğunlaşmağa imkan verir. Onun istismarı sadədir, nisbətən aşağı texniki tələblər, kütləvi istehsalda populyarlığını daha da artırır. Bundan əlavə, lazer kəsmə kimi digər kəsmə üsulları ilə müqayisədə mexaniki kəsmə daha çox idarə olunan xərclərə malikdir, bu da onu yüksək həcmli istehsal ehtiyacları üçün uyğun edir.
Məhdudiyyətlər
Çoxsaylı üstünlüklərinə baxmayaraq, mexaniki kəsmə texnologiyasının da məhdudiyyətləri var. Birincisi, alət və gofret arasındakı fiziki təmas səbəbindən, kəsmə dəqiqliyi nisbətən məhduddur, tez-tez çiplərin sonrakı qablaşdırılması və sınaqlarının düzgünlüyünə təsir göstərə bilən ölçülü sapmalara səbəb olur. İkincisi, mexaniki kəsmə prosesi zamanı qırılma və çatlar kimi qüsurlar asanlıqla baş verə bilər ki, bu da təkcə məhsuldarlığa təsir etmir, həm də çiplərin etibarlılığına və xidmət müddətinə mənfi təsir göstərə bilər. Mexanik gərginlikdən qaynaqlanan zərər xüsusilə yüksək sıxlıqlı çip istehsalı üçün zərərlidir, xüsusən də bu məsələlərin daha qabarıq olduğu kövrək materialları kəsərkən.
Texnoloji Təkmilləşdirmələr
Bu məhdudiyyətləri aradan qaldırmaq üçün tədqiqatçılar mexaniki kəsmə prosesini davamlı olaraq optimallaşdırırlar. Əsas təkmilləşdirmələrə kəsmə dəqiqliyini və dayanıqlığını artırmaq üçün daşlama çarxlarının dizaynının və material seçiminin təkmilləşdirilməsi daxildir. Bundan əlavə, kəsici avadanlığın struktur dizaynı və idarəetmə sistemlərinin optimallaşdırılması kəsmə prosesinin dayanıqlığını və avtomatlaşdırılmasını daha da yaxşılaşdırmışdır. Bu irəliləyişlər insan əməliyyatları nəticəsində yaranan səhvləri azaldır və kəsiklərin ardıcıllığını yaxşılaşdırır. Kəsmə prosesi zamanı anomaliyaların real vaxt rejimində monitorinqi üçün qabaqcıl yoxlama və keyfiyyətə nəzarət texnologiyalarının tətbiqi də kəsmə etibarlılığını və məhsuldarlığı əhəmiyyətli dərəcədə yaxşılaşdırmışdır.
Gələcək İnkişaf və Yeni Texnologiyalar
Mexanik kəsmə texnologiyası hələ də vafli kəsilməsində əhəmiyyətli bir mövqe tutsa da, yarımkeçirici proseslər inkişaf etdikcə yeni kəsmə texnologiyaları sürətlə inkişaf edir. Məsələn, termal lazer kəsmə texnologiyasının tətbiqi mexaniki kəsmədə dəqiqlik və qüsur məsələlərinə yeni həllər təqdim edir. Bu təmassız kəsmə üsulu vafli üzərində fiziki gərginliyi azaldır, xüsusilə daha kövrək materialların kəsilməsi zamanı qırılma və çatlama hallarını əhəmiyyətli dərəcədə azaldır. Gələcəkdə mexaniki kəsmə texnologiyasının yeni yaranan kəsmə üsulları ilə inteqrasiyası yarımkeçirici istehsalına daha çox seçim və çeviklik verəcək, istehsal səmərəliliyini və çip keyfiyyətini daha da artıracaq.
Yekun olaraq qeyd edək ki, mexaniki kəsmə texnologiyasının müəyyən çatışmazlıqları olsa da, davamlı texnoloji təkmilləşdirmələr və onun yeni kəsmə üsulları ilə inteqrasiyası yarımkeçiricilərin istehsalında hələ də mühüm rol oynamağa və gələcək proseslərdə rəqabət qabiliyyətini qoruyub saxlamağa imkan verir.
2.2 Lazerlə kəsmə texnologiyası
Lazer kəsmə texnologiyası vafli kəsilməsində yeni üsul kimi yüksək dəqiqliyi, mexaniki təmasın zədələnməməsi və sürətli kəsmə imkanlarına görə tədricən yarımkeçiricilər sənayesində geniş diqqət qazanmışdır. Bu texnologiya vafli materialın səthində kiçik istilik təsirinə məruz qalan zona yaratmaq üçün lazer şüasının yüksək enerji sıxlığı və fokuslanma qabiliyyətindən istifadə edir. Lazer şüası vafliyə tətbiq edildikdə, yaranan istilik gərginliyi materialın təyin olunmuş yerdə qırılmasına səbəb olur və dəqiq kəsmə əldə edilir.
Lazerlə kəsmə texnologiyasının üstünlükləri
• Yüksək Dəqiqlik: Lazer şüasının dəqiq yerləşdirmə qabiliyyəti müasir yüksək dəqiqlikli, yüksək sıxlıqlı inteqral sxem istehsalının tələblərinə cavab verən mikron və hətta nanometr səviyyəsində kəsmə dəqiqliyinə imkan verir.
• Mexanik əlaqə yoxdur: Lazerlə kəsmə vafli ilə fiziki təmasdan qaçır, mexaniki kəsmə zamanı qırılma və krekinq kimi ümumi problemlərin qarşısını alır, çiplərin məhsuldarlığını və etibarlılığını əhəmiyyətli dərəcədə artırır.
• Sürətli kəsmə sürəti: Lazer kəsmənin yüksək sürəti istehsalın səmərəliliyinin artmasına kömək edir və onu xüsusilə irimiqyaslı, yüksək sürətli istehsal ssenariləri üçün uyğun edir.
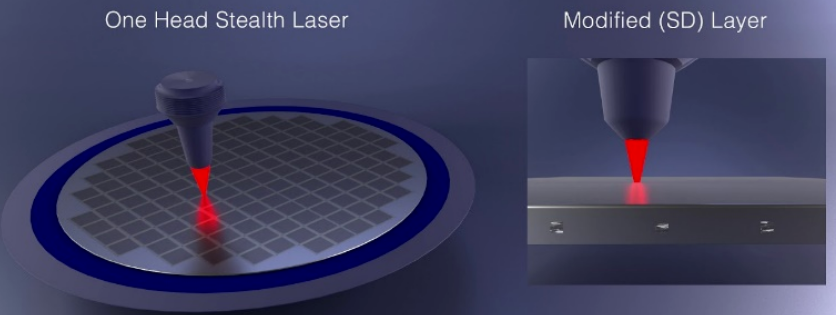
Qarşılaşılan Problemlər
• Yüksək Avadanlıq Qiyməti: Lazer kəsmə avadanlığı üçün ilkin investisiya yüksəkdir və bu, xüsusilə kiçik və orta ölçülü istehsal müəssisələri üçün iqtisadi təzyiq yaradır.
• Kompleks Prosesə Nəzarət: Lazerlə kəsmə enerji sıxlığı, fokus mövqeyi və kəsmə sürəti daxil olmaqla bir neçə parametrə dəqiq nəzarət tələb edir, bu da prosesi mürəkkəbləşdirir.
• İstilikdən Təsirə məruz qalan Zona Məsələləri: Lazer kəsmənin təmassız təbiəti mexaniki zədələri azaltsa da, istilikdən təsirlənən zonanın (HAZ) yaratdığı istilik gərginliyi vafli materialın xüsusiyyətlərinə mənfi təsir göstərə bilər. Bu effekti minimuma endirmək üçün prosesin əlavə optimallaşdırılması lazımdır.
Texnoloji Təkmilləşdirmə İstiqamətləri
Bu problemləri həll etmək üçün tədqiqatçılar avadanlıqların xərclərini azaltmağa, kəsmə səmərəliliyini artırmağa və proses axınının optimallaşdırılmasına diqqət yetirirlər.
• Effektiv Lazerlər və Optik Sistemlər: Daha səmərəli lazerlər və qabaqcıl optik sistemlər inkişaf etdirməklə, kəsmə dəqiqliyini və sürətini artırarkən avadanlıq xərclərini azaltmaq mümkündür.
• Proses Parametrlərinin Optimallaşdırılması: İstilikdən təsirlənən zonanı azaldan və bununla da kəsmə keyfiyyətini yaxşılaşdıran prosesləri təkmilləşdirmək üçün lazerlər və vafli materialları arasında qarşılıqlı əlaqəyə dair dərin tədqiqat aparılır.
• Ağıllı İdarəetmə Sistemləri: Ağıllı idarəetmə texnologiyalarının inkişafı lazer kəsmə prosesini avtomatlaşdırmaq və optimallaşdırmaq, onun sabitliyini və ardıcıllığını artırmaq məqsədi daşıyır.
Lazer kəsmə texnologiyası xüsusilə ultra nazik vaflilərdə və yüksək dəqiqlikli kəsmə ssenarilərində effektivdir. Vafli ölçüləri artdıqca və dövrə sıxlığı artdıqca, ənənəvi mexaniki kəsmə üsulları müasir yarımkeçirici istehsalının yüksək dəqiqlik və yüksək səmərəlilik tələblərinə cavab vermək üçün mübarizə aparır. Unikal üstünlüklərinə görə lazer kəsmə bu sahələrdə üstünlük verilən həll yoluna çevrilir.
Lazer kəsmə texnologiyası hələ də yüksək avadanlıq xərcləri və prosesin mürəkkəbliyi kimi problemlərlə üzləşsə də, yüksək dəqiqlik və təmassız zədələnmədə onun unikal üstünlükləri onu yarımkeçirici istehsalında inkişaf üçün mühüm istiqamətə çevirir. Lazer texnologiyası və ağıllı idarəetmə sistemləri irəliləməyə davam etdikcə, lazer kəsmənin yarımkeçirici sənayenin davamlı inkişafına təkan verərək, vafli kəsmə səmərəliliyini və keyfiyyətini daha da yaxşılaşdıracağı gözlənilir.
2.3 Plazma kəsmə texnologiyası
Plazma kəsmə texnologiyası, yeni yaranan gofret dilimləmə üsulu olaraq, son illərdə əhəmiyyətli diqqət qazanmışdır. Bu texnologiya plazma şüasının enerjisini, sürətini və kəsmə yolunu idarə edərək, optimal kəsmə nəticələrinə nail olmaqla vafliləri dəqiq şəkildə kəsmək üçün yüksək enerjili plazma şüalarından istifadə edir.
İş prinsipi və üstünlükləri
Plazma kəsmə prosesi avadanlıq tərəfindən yaradılan yüksək temperaturlu, yüksək enerjili plazma şüasına əsaslanır. Bu şüa vafli materialı çox qısa müddətdə ərimə və ya buxarlanma nöqtəsinə qədər qızdıra bilər və bu, sürətli kəsməyə imkan verir. Ənənəvi mexaniki və ya lazer kəsmə ilə müqayisədə, plazma kəsmə daha sürətli olur və daha kiçik istilikdən təsirlənən zona yaradır, kəsmə zamanı çatların və zədələnmələrin baş verməsini effektiv şəkildə azaldır.
Praktik tətbiqlərdə plazma kəsmə texnologiyası mürəkkəb formalı vaflilərlə işləmək üçün xüsusilə bacarıqlıdır. Onun yüksək enerjili, tənzimlənən plazma şüası nizamsız formalı vafliləri yüksək dəqiqliklə asanlıqla kəsə bilir. Buna görə də, mikroelektronika istehsalında, xüsusilə yüksək səviyyəli çiplərin fərdi və kiçik partiyalı istehsalında, bu texnologiya geniş istifadə üçün böyük vədlər verir.
Çağırışlar və Məhdudiyyətlər
Plazma kəsmə texnologiyasının bir çox üstünlüklərinə baxmayaraq, bəzi çətinliklərlə də üzləşir.
• Mürəkkəb Proses: Plazma kəsmə prosesi mürəkkəbdir və təmin etmək üçün yüksək dəqiqlikli avadanlıq və təcrübəli operatorlar tələb olunurkəsmədə dəqiqlik və sabitlik.
• Ətraf Mühitə Nəzarət və Təhlükəsizlik: Plazma şüasının yüksək temperaturlu, yüksək enerjili təbiəti ciddi ekoloji nəzarət və təhlükəsizlik tədbirləri tələb edir ki, bu da tətbiqin mürəkkəbliyini və dəyərini artırır.
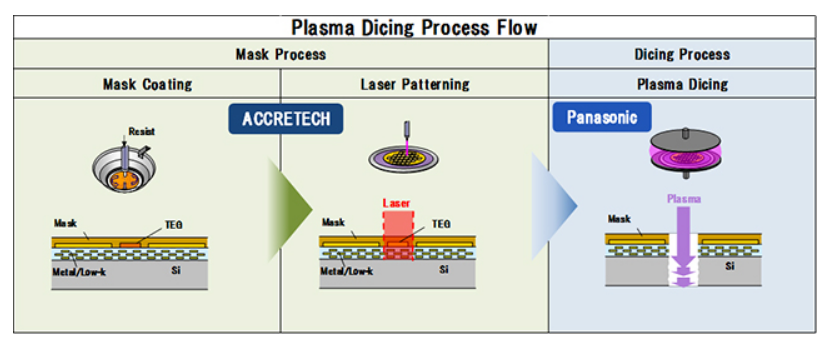
Gələcək İnkişaf İstiqamətləri
Texnoloji irəliləyişlərlə plazma kəsmə ilə bağlı problemlərin tədricən aradan qaldırılması gözlənilir. Daha ağıllı və daha dayanıqlı kəsici avadanlığın yaradılması ilə əl əməliyyatlarından asılılığı azaltmaq və bununla da istehsalın səmərəliliyini artırmaq olar. Eyni zamanda, proses parametrlərinin və kəsmə mühitinin optimallaşdırılması təhlükəsizlik risklərini və əməliyyat xərclərini azaltmağa kömək edəcək.
Yarımkeçiricilər sənayesində vafli kəsmə və dilimləmə texnologiyasındakı yeniliklər sənayenin inkişafına təkan vermək üçün çox vacibdir. Plazma kəsmə texnologiyası, yüksək dəqiqliyi, səmərəliliyi və mürəkkəb vafli formaları idarə etmək qabiliyyəti ilə bu sahədə əhəmiyyətli bir yeni oyunçu kimi ortaya çıxdı. Bəzi problemlər qalmasına baxmayaraq, bu problemlər davamlı texnoloji innovasiyalarla tədricən həll olunacaq və yarımkeçiricilər istehsalına daha çox imkan və imkanlar gətirəcək.
Plazma kəsmə texnologiyasının tətbiqi perspektivləri genişdir və onun gələcəkdə yarımkeçirici istehsalında daha mühüm rol oynayacağı gözlənilir. Davamlı texnoloji yeniliklər və optimallaşdırma sayəsində plazma kəsmə təkcə mövcud problemləri həll etməyəcək, həm də yarımkeçirici sənayenin inkişafının güclü sürücüsünə çevriləcək.
2.4 Kəsmə keyfiyyəti və təsir edən amillər
Vafli kəsmə keyfiyyəti sonrakı çip qablaşdırma, sınaq və son məhsulun ümumi performansı və etibarlılığı üçün çox vacibdir. Kəsmə zamanı rast gəlinən ümumi problemlərə çatlar, qırılmalar və kəsmə sapmaları daxildir. Bu problemlərə birlikdə işləyən bir neçə amil təsir edir.
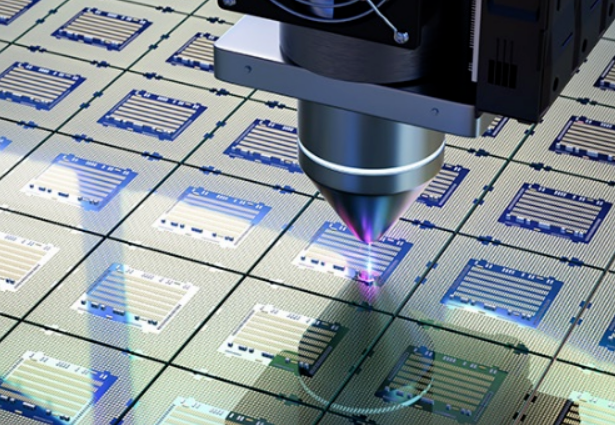
Kateqoriya | Məzmun | Təsir |
Proses Parametrləri | Kəsmə sürəti, yem sürəti və kəsmə dərinliyi birbaşa kəsmə prosesinin sabitliyinə və dəqiqliyinə təsir göstərir. Yanlış parametrlər gərginliyin konsentrasiyasına və həddindən artıq istidən təsirlənən zonaya gətirib çıxara bilər, nəticədə çatlar və çiplər yaranır. Vafli materialına, qalınlığına və kəsmə tələblərinə əsaslanaraq parametrlərin müvafiq şəkildə tənzimlənməsi istənilən kəsmə nəticələrinə nail olmaq üçün açardır. | Doğru proses parametrləri dəqiq kəsməni təmin edir və çatlar və qırılmalar kimi qüsurların riskini azaldır. |
Avadanlıq və Material Faktorları | -Bıçaq keyfiyyəti: Bıçağın materialı, sərtliyi və aşınma müqaviməti kəsmə prosesinin hamarlığına və kəsilmiş səthin düzlüyünə təsir göstərir. Keyfiyyətsiz bıçaqlar sürtünmə və istilik gərginliyini artırır, potensial olaraq çatlara və ya qırılmalara səbəb olur. Bıçaq üçün düzgün material seçmək çox vacibdir. -Soyuducu Performans: Soyuducu maddələr kəsmə temperaturunu azaltmağa, sürtünməni minimuma endirməyə və zibilləri təmizləməyə kömək edir. Effektiv olmayan soyuducu yüksək temperaturlara və zibil yığılmasına səbəb ola bilər, bu da kəsmə keyfiyyətinə və səmərəliliyinə təsir göstərir. Effektiv və ekoloji cəhətdən təmiz soyuducuların seçilməsi çox vacibdir. | Bıçağın keyfiyyəti kəsilmənin dəqiqliyinə və hamarlığına təsir göstərir. Səmərəsiz soyuducu aşağı kəsmə keyfiyyəti və səmərəliliyi ilə nəticələnə bilər, bu da optimal soyuducu istifadə ehtiyacını vurğulayır. |
Prosesə Nəzarət və Keyfiyyət Təftişi | -Prosesə Nəzarət: Kəsmə prosesində sabitliyi və ardıcıllığı təmin etmək üçün əsas kəsmə parametrlərinin real vaxt rejimində monitorinqi və tənzimlənməsi. -Keyfiyyət yoxlaması: Kəsmə sonrası görünüş yoxlamaları, ölçü ölçmələri və elektrik performans testləri keyfiyyət problemlərini dərhal müəyyən etməyə və həll etməyə kömək edir, kəsmə dəqiqliyini və ardıcıllığını artırır. | Prosesə düzgün nəzarət və keyfiyyət yoxlaması ardıcıl, yüksək keyfiyyətli kəsmə nəticələrini təmin etməyə və potensial problemlərin erkən aşkarlanmasına kömək edir. |

Kəsmə keyfiyyətinin yaxşılaşdırılması
Kəsmə keyfiyyətinin yaxşılaşdırılması proses parametrlərini, avadanlıq və material seçimini, prosesə nəzarəti və yoxlamanı nəzərə alan kompleks yanaşma tələb edir. Kəsmə texnologiyalarını davamlı olaraq təkmilləşdirmək və proses metodlarını optimallaşdırmaqla vafli kəsmənin dəqiqliyi və sabitliyi daha da artırıla bilər və yarımkeçiricilər istehsalı sənayesi üçün daha etibarlı texniki dəstək təmin edilə bilər.
# 03 Kəsmədən sonrakı iş və sınaq
3.1 Təmizləmə və Qurutma
Gofretin kəsilməsindən sonra təmizləmə və qurutma mərhələləri çip keyfiyyətini və sonrakı proseslərin düzgün gedişatını təmin etmək üçün vacibdir. Bu mərhələdə kəsmə zamanı yaranan silikon qalıqlarını, soyuducu qalıqlarını və digər çirkləndiriciləri hərtərəfli təmizləmək vacibdir. Təmizləmə prosesi zamanı çiplərin zədələnməməsini təmin etmək və quruduqdan sonra korroziya və ya elektrostatik boşalma kimi problemlərin qarşısını almaq üçün çip səthində nəmin qalmamasını təmin etmək eyni dərəcədə vacibdir.
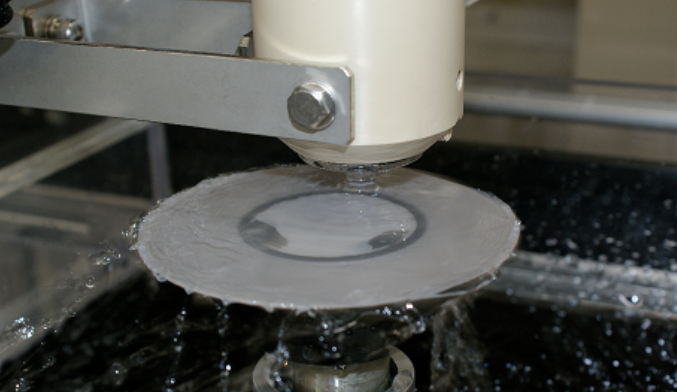
Kəsmə sonrası işləmə: Təmizləmə və Qurutma Prosesi
Proses addımı | Məzmun | Təsir |
Təmizləmə Prosesi | -Metod: Təmizləmə üçün ultrasəs və ya mexaniki fırçalama üsulları ilə birlikdə xüsusi təmizləyici vasitələrdən və təmiz sudan istifadə edin. | Çirkləndiricilərin hərtərəfli çıxarılmasını təmin edir və təmizləmə zamanı çiplərin zədələnməsinin qarşısını alır. |
-Təmizləyici agent seçimi: Çipə zərər vermədən effektiv təmizləmə təmin etmək üçün vafli materialı və çirkləndirici növü əsasında seçin. | Düzgün agent seçimi effektiv təmizləmə və çipdən qorunmaq üçün açardır. | |
-Parametrlərə nəzarət: Düzgün təmizlənmədən yaranan keyfiyyət problemlərinin qarşısını almaq üçün təmizləmə temperaturu, vaxtı və təmizləmə məhlulunun konsentrasiyasına ciddi nəzarət edin. | Nəzarətlər vaflinin zədələnməsinin qarşısını almağa və ya çirkləndiriciləri geridə qoymağa kömək edərək, ardıcıl keyfiyyəti təmin edir. | |
Qurutma Prosesi | -Ənənəvi üsullar: Təbii hava qurutma və isti hava ilə qurutma, aşağı səmərəliliyə malikdir və statik elektrik yığılmasına səbəb ola bilər. | Daha yavaş qurutma müddətləri və potensial statik problemlərlə nəticələnə bilər. |
-Müasir Texnologiyalar: Çiplərin tez qurumasını və zərərli təsirlərin qarşısını almaq üçün vakuum qurutma və infraqırmızı qurutma kimi qabaqcıl texnologiyalardan istifadə edin. | Daha sürətli və daha səmərəli qurutma prosesi, statik boşalma və ya nəmlə bağlı problemlər riskini azaldır. | |
Avadanlığın Seçilməsi və Baxımı | -Avadanlıq seçimi: Yüksək performanslı təmizləmə və qurutma maşınları emal səmərəliliyini artırır və işləmə zamanı yarana biləcək problemləri zərif şəkildə idarə edir. | Yüksək keyfiyyətli maşınlar daha yaxşı emal təmin edir və təmizləmə və qurutma zamanı xətaların baş vermə ehtimalını azaldır. |
-Avadanlıqlara texniki qulluq: Avadanlıqların müntəzəm yoxlanılması və texniki xidməti onun optimal iş şəraitində qalmasını təmin edir və çip keyfiyyətinə zəmanət verir. | Düzgün qulluq avadanlıqların nasazlığının qarşısını alır, etibarlı və yüksək keyfiyyətli emal təmin edir. |
Kəsmədən Sonra Təmizləmə və Qurutma
Vafli kəsildikdən sonra təmizləmə və qurutma mərhələləri son emal nəticəsini təmin etmək üçün bir çox amillərin diqqətlə nəzərdən keçirilməsini tələb edən mürəkkəb və incə proseslərdir. Elmi metodlardan və ciddi prosedurlardan istifadə etməklə, hər bir çipin optimal vəziyyətdə sonrakı qablaşdırma və sınaq mərhələlərinə daxil olmasını təmin etmək mümkündür.
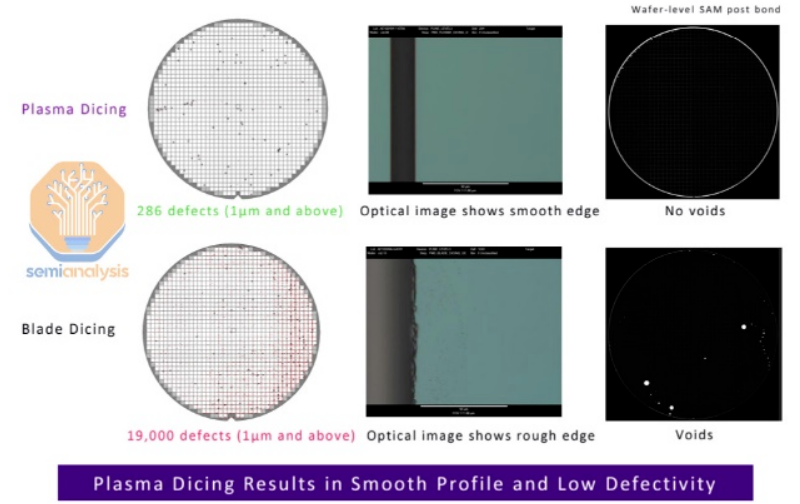
Kəsmə sonrası yoxlama və sınaq
addım | Məzmun | Təsir |
Yoxlama addımı | 1.Vizual Təftiş: Çip səthində çatlar, qırılmalar və ya çirklənmə kimi görünən qüsurları yoxlamaq üçün vizual və ya avtomatlaşdırılmış yoxlama avadanlıqlarından istifadə edin. Tullantıların qarşısını almaq üçün fiziki cəhətdən zədələnmiş çipləri tez müəyyənləşdirin. | Qüsurlu çipləri prosesin əvvəlində müəyyən etməyə və aradan qaldırmağa kömək edir, material itkisini azaldır. |
2.Ölçü Ölçüsü: Çip ölçülərini dəqiq ölçmək, kəsik ölçüsünün dizayn spesifikasiyalarına uyğun olmasını təmin etmək və performans problemlərinin və ya qablaşdırma çətinliklərinin qarşısını almaq üçün dəqiq ölçmə cihazlarından istifadə edin. | Çiplərin tələb olunan ölçü hədləri daxilində olmasını təmin edərək, performansın pisləşməsinin və ya montaj problemlərinin qarşısını alır. | |
3.Elektrik Performans Testi: Müqavimət, tutum və endüktans kimi əsas elektrik parametrlərini qiymətləndirin, uyğun olmayan çipləri müəyyən edin və yalnız performansa uyğun çiplərin növbəti mərhələyə keçməsini təmin edin. | Yalnız funksional və performans testindən keçmiş çiplərin prosesdə irəliləməsini təmin edir, sonrakı mərhələlərdə uğursuzluq riskini azaldır. | |
Test addımı | 1.Funksional sınaq: Çipin əsas funksionallığının nəzərdə tutulduğu kimi işlədiyini yoxlayın, funksional anormallıqları olan çipləri müəyyənləşdirin və aradan qaldırın. | Sonrakı mərhələlərə keçməzdən əvvəl çiplərin əsas əməliyyat tələblərinə cavab verməsini təmin edir. |
2.Etibarlılıq Testi: Uzun müddət istifadə və ya sərt mühitlərdə çip performansının sabitliyini qiymətləndirin, adətən yüksək temperaturda yaşlanma, aşağı temperatur testi və real dünyadakı ekstremal şəraiti simulyasiya etmək üçün rütubət testi daxildir. | Çiplərin müxtəlif ekoloji şəraitdə etibarlı şəkildə işləməsini təmin edir, məhsulun uzunömürlülüyünü və dayanıqlığını artırır. | |
3.Uyğunluq Testi: Uyğunsuzluq səbəbindən heç bir nasazlıq və ya performansın azalmasının olmadığından əmin olaraq, çipin digər komponentlər və ya sistemlərlə düzgün işlədiyini yoxlayın. | Uyğunluq problemlərinin qarşısını alaraq real dünya tətbiqlərində düzgün işləməyi təmin edir. |
3.3 Qablaşdırma və Saxlama
Gofret kəsildikdən sonra, çiplər yarımkeçirici istehsal prosesinin mühüm məhsuludur və onların qablaşdırılması və saxlanması mərhələləri də eyni dərəcədə vacibdir. Düzgün qablaşdırma və saxlama tədbirləri təkcə daşınma və saxlama zamanı çiplərin təhlükəsizliyini və dayanıqlığını təmin etmək üçün deyil, həm də sonrakı istehsal, sınaq və qablaşdırma mərhələlərinə güclü dəstək vermək üçün vacibdir.
Yoxlama və Sınaq Mərhələlərinin xülasəsi:
Vafli kəsildikdən sonra çiplər üçün yoxlama və sınaq mərhələləri vizual yoxlama, ölçü ölçmə, elektrik performans testi, funksional sınaq, etibarlılıq testi və uyğunluq testi daxil olmaqla bir sıra aspektləri əhatə edir. Bu addımlar bir-birinə bağlıdır və bir-birini tamamlayır, məhsulun keyfiyyətini və etibarlılığını təmin etmək üçün möhkəm maneə yaradır. Ciddi yoxlama və sınaq prosedurları vasitəsilə son məhsulun müştəri tələblərinə və gözləntilərinə cavab verməsini təmin etməklə potensial problemlər dərhal müəyyən edilə və həll edilə bilər.
Aspekt | Məzmun |
Qablaşdırma tədbirləri | 1.Antistatik: Qablaşdırma materialları statik elektrikin cihazlara zərər verməsinin və ya onların işinə təsir etməsinin qarşısını almaq üçün əla antistatik xüsusiyyətlərə malik olmalıdır. |
2.Nəmə davamlı: Rütubət nəticəsində yaranan korroziyanın və elektrik performansının pisləşməsinin qarşısını almaq üçün qablaşdırma materialları yaxşı nəmə davamlılığa malik olmalıdır. | |
3.Zərbəyə davamlı: Qablaşdırma materialları daşınma zamanı çipləri vibrasiyadan və təsirdən qorumaq üçün təsirli zərbə udma təmin etməlidir. | |
Saxlama Mühiti | 1.Rütubətə Nəzarət: Həddindən artıq rütubətin və ya aşağı rütubətin səbəb olduğu statik problemlərin səbəb olduğu rütubətin udulmasının və korroziyanın qarşısını almaq üçün müvafiq diapazonda rütubətə ciddi şəkildə nəzarət edin. |
2.Təmizlik: Çiplərin toz və çirklərlə çirklənməsinin qarşısını almaq üçün təmiz saxlama mühitini qoruyun. | |
3.Temperatur nəzarəti: Aşağı temperaturun səbəb olduğu həddindən artıq istilik və ya kondensasiya problemləri səbəbindən sürətlənmiş yaşlanmanın qarşısını almaq üçün ağlabatan temperatur diapazonunu təyin edin və temperatur sabitliyini qoruyun. | |
Daimi Yoxlama | Potensial problemləri vaxtında müəyyən etmək və həll etmək üçün vizual yoxlamalar, ölçü ölçmələri və elektrik performans testlərindən istifadə edərək, saxlanılan çipləri müntəzəm olaraq yoxlayın və qiymətləndirin. Saxlama müddətinə və şərtlərinə əsasən, çiplərin optimal vəziyyətdə istifadə edilməsini təmin etmək üçün onların istifadəsini planlaşdırın. |
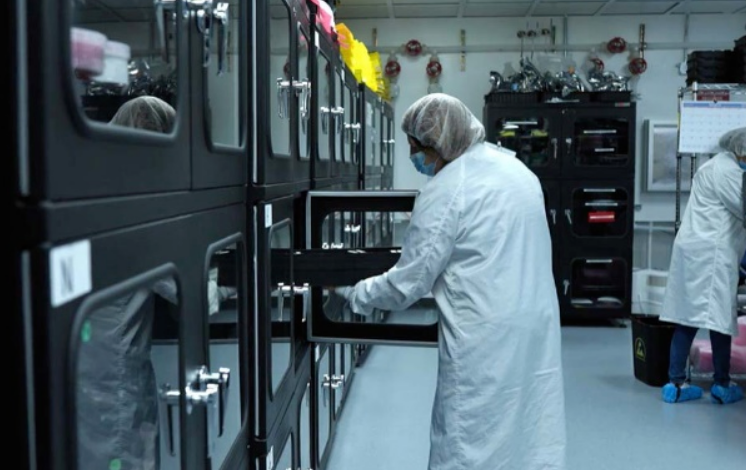
Yarımkeçiricilərin istehsalında vafli dilimləmə prosesi zamanı mikro çatlar və zədələnmələr məsələsi əhəmiyyətli problemdir. Kəsmə gərginliyi bu fenomenin əsas səbəbidir, çünki o, vafli səthində kiçik çatlar və zədələr yaradır, bu da istehsal xərclərinin artmasına və məhsulun keyfiyyətinin azalmasına səbəb olur.
Bu problemi həll etmək üçün kəsmə gərginliyini minimuma endirmək və optimallaşdırılmış kəsmə üsullarını, alətləri və şərtləri tətbiq etmək çox vacibdir. Bıçaq materialı, kəsmə sürəti, təzyiq və soyutma üsulları kimi amillərə diqqət yetirilməsi mikro çatların əmələ gəlməsini azaltmağa və prosesin ümumi məhsuldarlığını yaxşılaşdırmağa kömək edə bilər. Bundan əlavə, lazerlə kəsmə kimi daha qabaqcıl kəsmə texnologiyaları üzrə davam edən tədqiqatlar bu problemləri daha da yüngülləşdirməyin yollarını araşdırır.
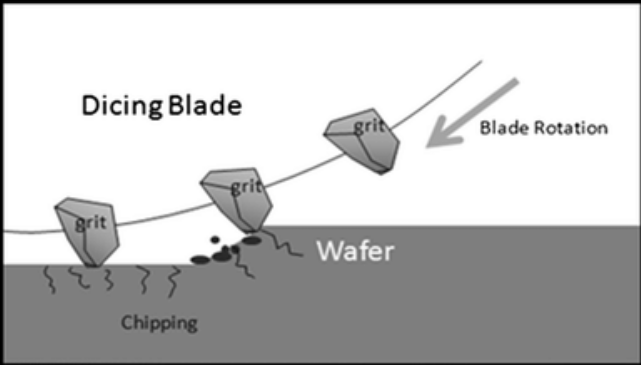
Kövrək bir material olaraq, vafli mexaniki, istilik və ya kimyəvi stresə məruz qaldıqda, mikro çatların meydana gəlməsinə səbəb olan daxili struktur dəyişikliklərinə meyllidir. Bu çatlar dərhal nəzərə çarpmasa da, istehsal prosesi irəlilədikcə genişlənə və daha ciddi zədələrə səbəb ola bilər. Temperaturun dəyişməsi və əlavə mexaniki gərginliklər bu mikroçatların görünən qırıqlara çevrilməsinə və potensial olaraq çip çatışmazlığına səbəb ola biləcəyi sonrakı qablaşdırma və sınaq mərhələlərində bu məsələ xüsusilə problemli olur.
Bu riski azaltmaq üçün kəsmə sürəti, təzyiq və temperatur kimi parametrləri optimallaşdırmaqla kəsmə prosesinə diqqətlə nəzarət etmək vacibdir. Lazerlə kəsmə kimi daha az aqressiv kəsmə üsullarından istifadə vaflidə mexaniki gərginliyi azalda və mikro çatların əmələ gəlməsini minimuma endirə bilər. Bundan əlavə, vafli dilimləmə prosesi zamanı infraqırmızı skan və ya rentgen təsviri kimi qabaqcıl yoxlama üsullarının tətbiqi bu erkən mərhələdə çatlaqları daha çox zərər verməzdən əvvəl aşkar etməyə kömək edə bilər.
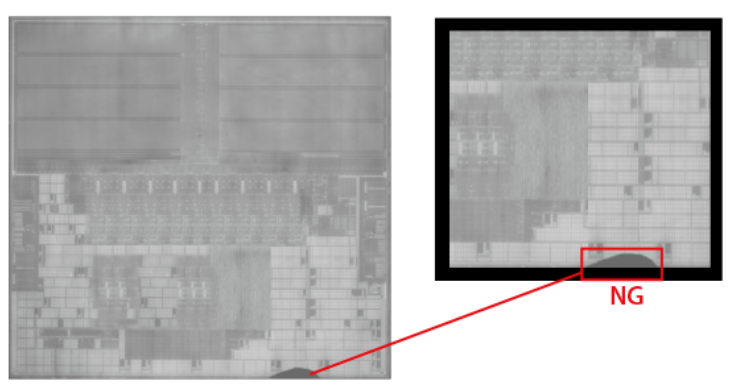
Gofret səthinin zədələnməsi küp kəsmə prosesində əhəmiyyətli narahatlıq doğurur, çünki bu, çipin performansına və etibarlılığına birbaşa təsir göstərə bilər. Belə zərər kəsici alətlərin düzgün istifadə edilməməsi, səhv kəsmə parametrləri və ya vaflinin özünə xas olan material qüsurları nəticəsində yarana bilər. Səbəbindən asılı olmayaraq, bu zədələr dövrənin elektrik müqavimətində və ya tutumunda dəyişikliklərə səbəb ola bilər və ümumi performansa təsir edə bilər.
Bu problemləri həll etmək üçün iki əsas strategiya araşdırılır:
1.Kəsici alətlərin və parametrlərin optimallaşdırılması: Daha kəskin bıçaqlardan istifadə etməklə, kəsmə sürətini tənzimləmək və kəsmə dərinliyini dəyişdirməklə, kəsmə prosesi zamanı gərginliyin konsentrasiyası minimuma endirilə bilər, beləliklə, zədələnmə potensialı azalır.
2. Yeni kəsmə texnologiyalarının araşdırılması: Lazer kəsmə və plazma kəsmə kimi qabaqcıl üsullar vaflidə vurulan zərərin səviyyəsini potensial olaraq azaldaraq, təkmilləşdirilmiş dəqiqlik təklif edir. Bu texnologiyalar vaflidə istilik və mexaniki gərginliyi minimuma endirməklə yüksək kəsmə dəqiqliyinə nail olmaq yollarını tapmaq üçün öyrənilir.
İstilik Təsir Sahəsi və Performansa Təsirləri
Lazer və plazma kəsmə kimi termal kəsmə proseslərində yüksək temperatur istər-istəməz vafli səthində termal təsir zonası yaradır. Temperatur qradiyentinin əhəmiyyətli olduğu bu sahə, çipin son performansına təsir edərək, materialın xüsusiyyətlərini dəyişə bilər.
Termal Təsirə məruz qalan Zonanın Təsiri (TAZ):
Kristal Struktur Dəyişiklikləri: Yüksək temperaturda vafli materialın içərisindəki atomlar yenidən yerləşə bilər və kristal strukturunda təhriflərə səbəb ola bilər. Bu təhrif materialı zəiflədir, onun mexaniki möhkəmliyini və dayanıqlığını azaldır, bu da istifadə zamanı çip çatışmazlığı riskini artırır.
Elektrik xassələrindəki dəyişikliklər: Yüksək temperaturlar yarımkeçirici materiallarda daşıyıcının konsentrasiyasını və hərəkətliliyini dəyişə bilər, çipin elektrik keçiriciliyinə və cərəyan ötürmə səmərəliliyinə təsir göstərir. Bu dəyişikliklər çipin performansının azalmasına gətirib çıxara bilər ki, bu da onu nəzərdə tutulmuş məqsəd üçün yararsız hala gətirir.
Bu təsirləri azaltmaq üçün kəsmə zamanı temperaturun idarə edilməsi, kəsmə parametrlərinin optimallaşdırılması və soyutma jetləri və ya emaldan sonrakı müalicə kimi üsulların araşdırılması istilik təsirinin dərəcəsini azaltmaq və materialın bütövlüyünü qorumaq üçün vacib strategiyalardır.
Ümumiyyətlə, həm mikro çatlar, həm də termal təsir zonaları vafli dilimləmə texnologiyasında həlledici problemlərdir. Yarımkeçirici məhsulların keyfiyyətinin yaxşılaşdırılması və bazarda rəqabət qabiliyyətinin yüksəldilməsi üçün texnoloji irəliləyişlər və keyfiyyətə nəzarət tədbirləri ilə yanaşı davamlı tədqiqatlar zəruri olacaqdır.
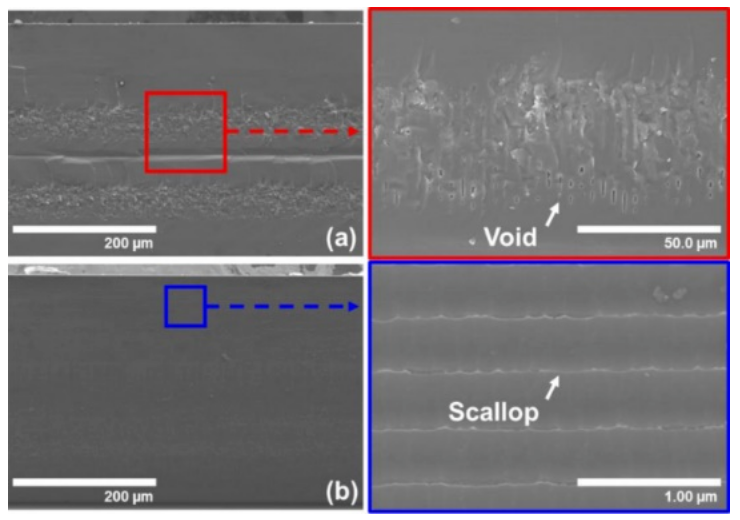
Termal Təsir Zonasına Nəzarət Tədbirləri:
Kəsmə prosesi parametrlərinin optimallaşdırılması: Kəsmə sürətinin və gücünün azaldılması istilik təsir zonasının (TAZ) ölçüsünü effektiv şəkildə minimuma endirə bilər. Bu, vaflinin material xüsusiyyətlərinə birbaşa təsir edən kəsmə prosesi zamanı yaranan istilik miqdarını idarə etməyə kömək edir.
Qabaqcıl Soyutma Texnologiyaları: Maye azotla soyutma və mikrofluidik soyutma kimi texnologiyaların tətbiqi termal təsir zonasının diapazonunu əhəmiyyətli dərəcədə məhdudlaşdıra bilər. Bu soyutma üsulları istiliyin daha səmərəli şəkildə yayılmasına kömək edir, beləliklə, vaflinin material xüsusiyyətlərini qoruyur və istilik zərərini minimuma endirir.
Material seçimi: Tədqiqatçılar mükəmməl istilik keçiriciliyinə və mexaniki gücə malik olan karbon nanoborucuqları və qrafen kimi yeni materialları araşdırırlar. Bu materiallar çiplərin ümumi performansını yaxşılaşdırarkən termal təsir zonasını azalda bilər.
Xülasə, termal təsir zonası termal kəsmə texnologiyalarının qaçılmaz nəticəsi olsa da, optimallaşdırılmış emal üsulları və material seçimi ilə effektiv şəkildə idarə oluna bilər. Gələcək tədqiqatlar, çox güman ki, daha səmərəli və dəqiq vafli dilimlərə nail olmaq üçün termal kəsmə proseslərinin dəqiq tənzimlənməsinə və avtomatlaşdırılmasına yönəldiləcək.

Balans Strategiyası:
Gofret məhsuldarlığı və istehsal səmərəliliyi arasında optimal tarazlığa nail olmaq vafli dilimləmə texnologiyasında davamlı problemdir. İstehsalçılar rasional istehsal strategiyası və proses parametrlərini hazırlamaq üçün bazar tələbi, istehsal xərcləri və məhsulun keyfiyyəti kimi bir çox amilləri nəzərə almalıdırlar. Eyni zamanda, qabaqcıl kəsici avadanlıqların tətbiqi, operatorların bacarıqlarının təkmilləşdirilməsi və xammalın keyfiyyətinə nəzarətin gücləndirilməsi məhsuldarlığı qorumaq və hətta istehsal səmərəliliyini artırmaq üçün vacibdir.
Gələcək Çağırışlar və İmkanlar:
Yarımkeçirici texnologiyanın inkişafı ilə vafli kəsmə yeni problemlər və imkanlarla üzləşir. Çip ölçüləri kiçildikcə və inteqrasiya artdıqca kəsmə dəqiqliyinə və keyfiyyətinə olan tələblər əhəmiyyətli dərəcədə artır. Eyni zamanda, yaranan texnologiyalar vafli kəsmə texnikasının inkişafı üçün yeni ideyalar təqdim edir. İstehsalçılar bazar dinamikasına və texnoloji tendensiyalara uyğunlaşmalı, bazar dəyişikliklərinə və texnoloji tələblərə cavab vermək üçün istehsal strategiyalarını və proses parametrlərini davamlı olaraq tənzimləməli və optimallaşdırmalıdırlar.
Nəticə olaraq, bazar tələbi, istehsal xərcləri və məhsulun keyfiyyəti ilə bağlı mülahizələri birləşdirməklə və qabaqcıl avadanlıq və texnologiyanı tətbiq etməklə, operator bacarıqlarını artırmaqla və xammala nəzarəti gücləndirməklə, istehsalçılar vafli dilimləmə zamanı vafli məhsuldarlığı ilə istehsal səmərəliliyi arasında ən yaxşı tarazlığa nail ola bilərlər ki, bu da səmərəli və yüksək keyfiyyətli yarımkeçirici məhsul istehsalına səbəb olur.
Gələcək Outlook:
Sürətli texnoloji tərəqqi ilə yarımkeçirici texnologiya görünməmiş bir sürətlə irəliləyir. Yarımkeçiricilərin istehsalında kritik bir addım olaraq, vafli kəsmə texnologiyası maraqlı yeni inkişaflara hazırlaşır. Gələcəyə baxsaq, vafli kəsmə texnologiyasının dəqiqlik, səmərəlilik və xərclərdə əhəmiyyətli təkmilləşdirmələrə nail olacağı, yarımkeçirici sənayenin davamlı böyüməsinə yeni canlılıq gətirəcəyi gözlənilir.
Artan dəqiqlik:
Daha yüksək dəqiqliyə nail olmaq üçün vafli kəsmə texnologiyası davamlı olaraq mövcud proseslərin sərhədlərini itələyəcəkdir. Kəsmə prosesinin fiziki və kimyəvi mexanizmlərini dərindən öyrənmək və kəsmə parametrlərinə dəqiq nəzarət etməklə, getdikcə daha mürəkkəb dövrə dizayn tələblərinə cavab vermək üçün daha incə kəsmə nəticələri əldə ediləcək. Bundan əlavə, yeni materialların və kəsmə üsullarının kəşfi məhsuldarlığı və keyfiyyəti əhəmiyyətli dərəcədə yaxşılaşdıracaqdır.
Səmərəliliyin artırılması:
Yeni vafli kəsmə avadanlığı diqqəti ağıllı və avtomatlaşdırılmış dizayna yönəldəcək. Qabaqcıl idarəetmə sistemlərinin və alqoritmlərin tətbiqi avadanlıqlara müxtəlif materiallara və dizayn tələblərinə uyğun olaraq kəsmə parametrlərini avtomatik tənzimləməyə imkan verəcək və beləliklə, istehsalın səmərəliliyini əhəmiyyətli dərəcədə artıracaqdır. Çox vafli kəsmə texnologiyası və bıçaqların sürətli dəyişdirilməsi sistemləri kimi yeniliklər səmərəliliyin artırılmasında mühüm rol oynayacaq.
Xərclərin azaldılması:
Xərclərin azaldılması vafli kəsmə texnologiyasının inkişafı üçün əsas istiqamətdir. Yeni materiallar və kəsmə üsulları işlənib hazırlandıqca, avadanlıq xərclərinə və texniki xidmət xərclərinə effektiv şəkildə nəzarət edilməsi gözlənilir. Bundan əlavə, istehsal proseslərinin optimallaşdırılması və qırıntıların azaldılması istehsal zamanı tullantıları daha da azaldacaq və ümumi istehsal xərclərinin azalmasına səbəb olacaqdır.
Ağıllı İstehsalat və IoT:
Ağıllı istehsal və Əşyaların İnterneti (IoT) texnologiyalarının inteqrasiyası vafli kəsmə texnologiyasına transformativ dəyişikliklər gətirəcək. Cihazlar arasında qarşılıqlı əlaqə və məlumat mübadiləsi vasitəsilə istehsal prosesinin hər bir addımı real vaxt rejimində izlənilə və optimallaşdırıla bilər. Bu, nəinki istehsalın səmərəliliyini və məhsulun keyfiyyətini artırır, həm də şirkətlərə bazarın daha dəqiq proqnozlaşdırılması və qərarların qəbul edilməsinə dəstək verir.
Gələcəkdə vafli kəsmə texnologiyası dəqiqlik, səmərəlilik və qiymətdə nəzərəçarpacaq irəliləyişlər edəcək. Bu irəliləyişlər yarımkeçirici sənayenin davamlı inkişafına təkan verəcək və insan cəmiyyətinə daha çox texnoloji yeniliklər və rahatlıqlar gətirəcək.
Göndərmə vaxtı: 19 noyabr 2024-cü il